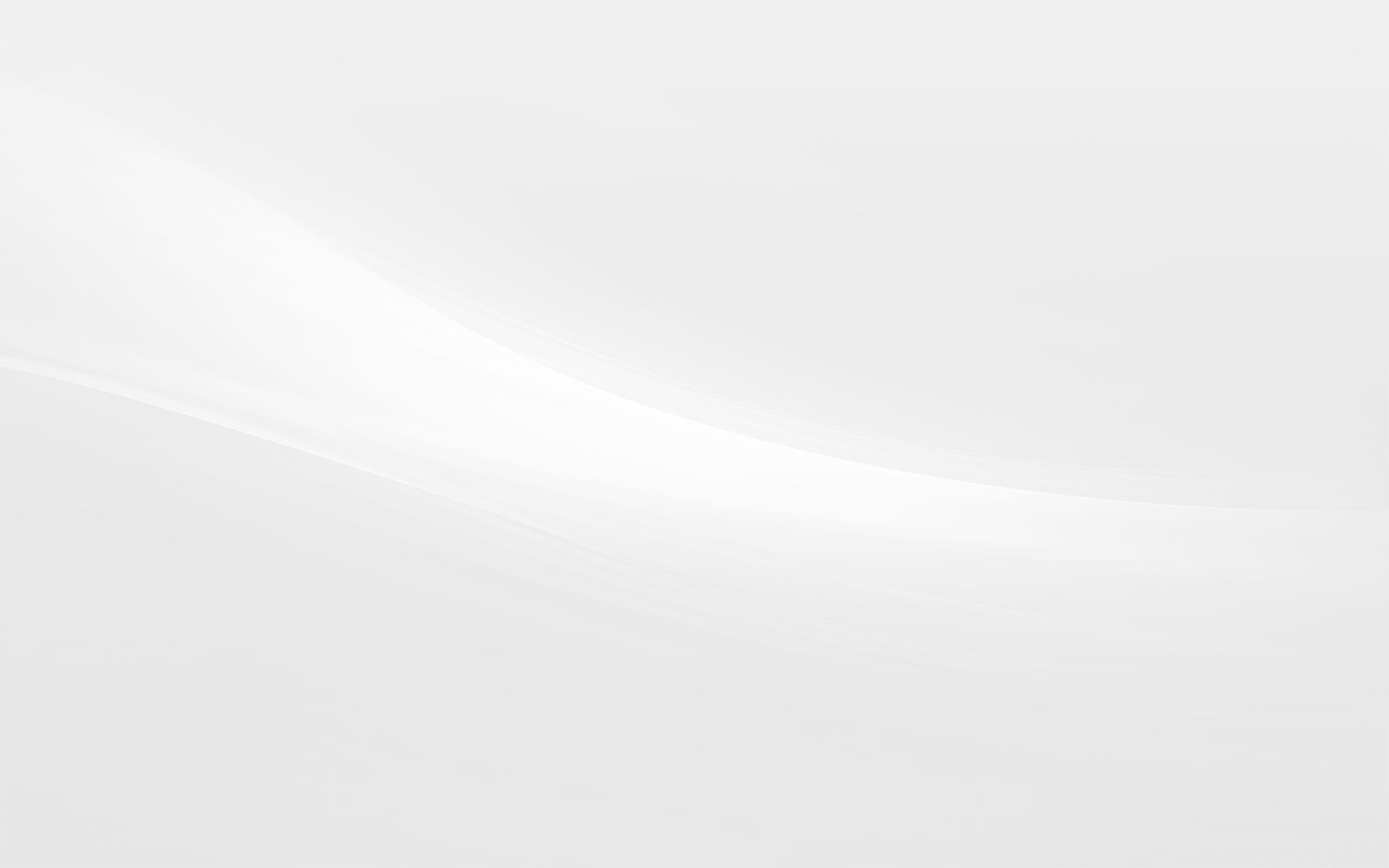
O que é Black Belt, 6-Sigma e Lean?
Black Belt - Dedicar tempo e conhecimento para entender os problemas e buscar melhorias para diminuir ou eliminar falhas que possam afetar a produtividade de uma empresa. Esta é a função básica dos Black Belts, profissionais especialmente treinados que lideram a aplicação das metodologias e ferramentas da filosofia Seis Sigma - uma parte do formato de gestão Lean (veja a matéria Para saber mais sobre o nascimento do lean). No entanto, é preciso lembrar que o Seis Sigma é um processo nascido na norte-americana Motorola, em 1986, diferente do Lean, que surgiu no Japão, dentro da Toyota, na década de 1970, por isso, possuem suas diferenças.
Os principais pontos que os dois processos trabalham na empresa são eliminação de perdas, redução de custos e melhoria na produtividade. Segundo Sammy Obara, consultor da Honsha Gestão Empresarial, essas mudanças no dia-a-dia da entidade costumam ter um impacto de, no mínimo, US$ 100 mil nas economias anuais - o que pode ser a diferença entre lucro e déficit. "A combinação entre a aplicação das metodologias com os resultados financeiros gerados são a base para a certificação do Black Belt", explica.
De acordo com Taiichi Ohno (1988): Os valores sociais mudaram. Agora, não podemos vender nossos produtos a não ser que nos coloquemos dentro dos corações de nossos consumidores, cada um dos quais tem conceitos e gostos diferentes. Hoje, o mundo industrial foi forçado a dominar de verdade o sistema de produção múltiplo, em pequenas quantidades.
A base de sustentação do Sistema Toyota de Produção é a absoluta eliminação do desperdício e os dois pilares necessários à sustentação é o just-in-time e a autonomação.
Os 7 desperdícios que o sistema visa a eliminar:
- Superprodução, a maior fonte de desperdício.
- Tempo de espera, refere-se a materiais que aguardam em filas para serem processados.
- Transporte, nunca geram valor agregado no produto.
- Processamento, algumas operações de um processo poderiam nem existir.
- Estoque, sua redução ocorrerá através de sua causa raiz.
- Movimentação
- Defeitos, produzir produtos defeituosos significa desperdiçar materiais, mão-de-obra, movimentação de materiais defeituosos e outros.
Ferramentas LEAN
- Para enxergar os problemas: Mapeamento de Fluxo de Valor, Gestão Visual, Monitoramento Hora a Hora, 5S...
- Para identificar a raiz/causas dos Problemas: 5 porquês com validação, diagrama de Ishikawa, A3...
- Para resolver os problemas: Desdobramento de objetivos estratégicos (hoshin kanri), KAIZEN, trabalho em equipe, .
Fundado em 1997 por James Womack e por Jonh Shook, com o intuito de disseminar o Sistema Lean, o Lean Institute tem como um de seus
principais papéis pesquisar as ferramentas Lean e adaptá-las para os contextos das empresas, auxiliando assim a implementação do Lean dentro
dos setores mais diversos.
É comum que as empresas iniciem sua jornada através do Mapeamento de Fluxo de Valor (MFV) para justamente aprender a enxergar os desperdícios do seu sistema produtivo e localizar os pontos mais críticos e planejar a melhoria do fluxo. Em seguida, costuma-se estudar a criação de Fluxo Contínuo ou Fluxo de uma peça (one piece flow) para redução dos desperdícios entre processos adjacentes, balanceamento da linha e redução do Lead Time. A sequência de implementação do sistema lean costuma incorporar também a cultura do Sistema Puxado Nivelado, que consolida a lógica de produção conectando a ordem de produção a real necessidade do cliente, produzindo apenas aquilo que realmente é consumido.
Outras características do sistema LEAN
Reunião de geração de ideias que adota a administração japonesa como filosofia de atuação.
- É uma abordagem bottom-up. O envolvimento dos colaboradores é determinante para o sucesso de projetos LEAN, pois são eles que melhor
conhecem os processos.
- É um ciclo que não acaba, numa lógica de melhoria contínua.
- O processo geração de ideias, viabilidade, implementação não é LEAN. Nos projetos LEAN, os grupos de trabalhos são orientados pelos 7
desperdícios acima referidos.
- Atua ao nível dos processos, das atitudes e comportamentos e das ferramentas de gestão.
O Sistema Toyota de Produção vem sendo implantado em várias empresas no mundo todo, porém nem sempre com grande sucesso. A dificuldade reside no aspecto cultural. Toda uma herança histórica e filosófica conferem uma singularidade ao modelo japonês.
Segundo matéria na Newsweek International, em 2005, a Toyota Motors Company obteve lucros recordes de US$ 11 bilhões, que ultrapassa os
ganhos da GM, Ford e DaimlerChrysler juntas.
Em 2007 a Toyota tornou-se a maior empresa automobilística do mundo, fato que só era previsto para 2008.

6Sigma - No processo Seis Sigma existem três tipos de profissionais especializados. Os Champions são diretores e gerentes que permitem colocar em prática os projetos desenvolvidos, e é exigido treinamento de 30 horas/aulas para ser graduado. Os Green Belts ajudam os Black Belts na implementação dos projetos, sem se dedicar exclusivamente ao processo Seis Sigma, possuindo formação em curso de 100 horas/aulas, mais desenvolvimento de projeto. Já os Black Belts se dedicam exclusivamente à filosofia Seis Sigma, são eles os responsáveis por todo o projeto, desde a ideia até a sua execução. Para ser um Black Belt é necessário ter certificação em curso de 200 horas/aulas, mais desenvolvimento de projeto.

Mais do que a certificação, para ser um Black Belt é preciso ser dinâmico, ter habilidade para acompanhar e executar projetos, ser hábil para efetuar e aceitar mudanças e ter capacidade de liderança. Como a maioria das publicações sobre o assunto são em inglês, possuir conhecimento da língua também é essencial.
Pela especialização que exigem e pelo retorno financeiro da aplicação da filosofia, os Black Belts são profissionais muito requisitados no mercado de trabalho. "O Six Sigma treina um grupo seleto de profissionais de uma empresa, que então se tornam responsáveis por grandes mudanças e melhorias através da implementação de ferramentas e técnicas, geralmente bastante complexas para que os trabalhadores da linha de frente possam usar cotidianamente".

Lean Manufacturing - O Sistema Toyota de Produção surgiu no Japão, na fábrica de automóveis Toyota, logo após a Segunda Guerra Mundial. Naquela época a indústria japonesa tinha uma produtividade muito baixa e uma enorme falta de recursos, o que a impedia de adotar o modelo da produção em massa. O Sistema Toyota de Produção também é chamado de Produção enxuta ou Lean Manufacturing. [carece de fontes]
A criação do Sistema Toyota de Produção se deve, principalmente, a quatro pessoas: O fundador da Toyota e mestre de invenções, Sakichi Toyoda, seu filho Kiichiro Toyoda, primo de Eiji Toyoda que participou como o executivo impulsionador do nascimento do STP (Sistema Toyota de Produção) e o engenheiro chefe da Toyota Motors Company, o chinês Taiichi Ohno. O sistema objetiva aumentar a eficiência da produção pela eliminação contínua de desperdícios.
O sistema de produção em massa desenvolvido por Frederick Taylor e Henry Ford no início do século XX predominou no mundo até a década de 90. Procurava reduzir os custos unitários dos produtos através da produção em larga escala, especialização e divisão do trabalho. Entretanto este sistema tinha que operar com estoques e lotes de produção elevados. No início não havia grande preocupação com a qualidade do produto.
Já no Sistema Toyota de Produção, os lotes de produção são pequenos, permitindo uma maior variedade de produtos. Exemplo: em vez de produzir um lote de 50 sedans brancos, produz-se 10 lotes com 5 veículos cada, com cores e modelos variados. Os trabalhadores são multifuncionais, ou seja, conhecem outras tarefas além de sua própria e sabem operar mais que uma única máquina. No Sistema Toyota de Produção a preocupação com a qualidade do produto é extrema. Foram desenvolvidas diversas técnicas simples mas extremamente eficientes para proporcionar os resultados esperados, como o Kanban e o Poka-Yoke.
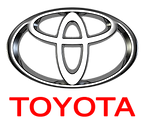